stepper motor is type of special machine that completes their rotation in stepwise . It especially designed to complete rotation step by so it is also known as stepping motor. In this article we will learn its construction and working principle.
Construction of stepper motor
stepper motor consist with two important part that is stator and rotor like other electric motors
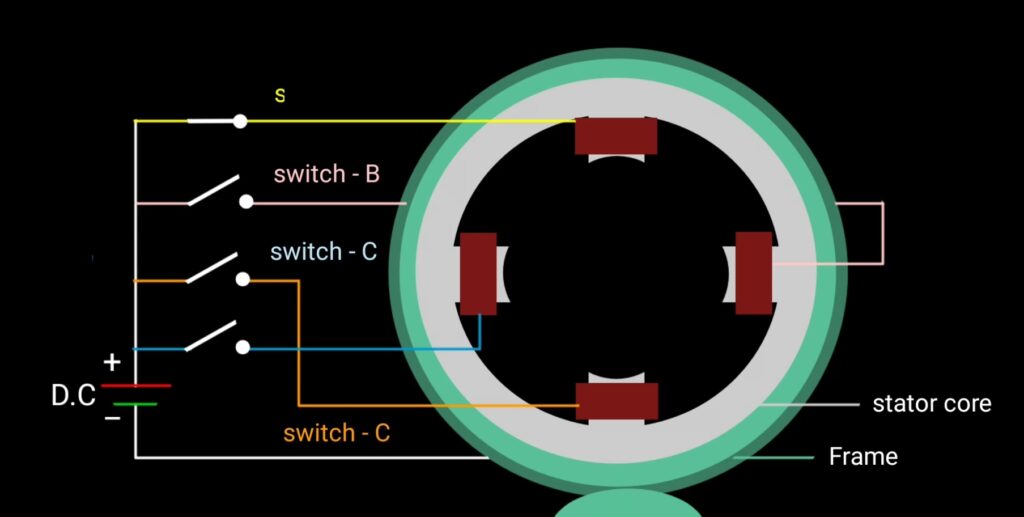
Stator core : Here it is stator core that have circular shape it can be also rectangular shape according to application we can design. Stator core is made up of laminated Silicon steel we use this material due to their high permeability that supports the magnetic field lines. Lamination is the arrangement of theen sheets that combined together to make a stator, each sheet have diameter of 0.33 mm.
We provide lamination to reduce Eddy current loss. Poles are present at the inner portion of stator winding that is made up of copper. We use copper material due to their good electrical conductivity. Stator pole can be different like 4-pole , 8-pole .. etc according to application.
Stator frame : Frame protects the stator core and main parts of the stepper motor from mechanical damage and frame is made up of cast iron that provide mechanical support to the internal assembly and important part of the machine.
as you can see in above diagram how do we make connection of stepper motor, each stator phase innergize separately by using separate switches
permanent magnet rotor is used in stepper motor due to absence of brushes and commutator like bldc motor so we use permanent magnet
We select that type of magnetic material for making rotor which have more flux density to achieve maximum torque so generally we use ferromagnetic material like Iron , Nickel , Cobalt etc that provide required torque. In above diagram I have considered two pole rotor it can be more according to application.
Working principle of stepper motor
first of all we give DC supply to the stepper motor. Suppose in starting switch-A is (ON) and another switches remain (OFF).
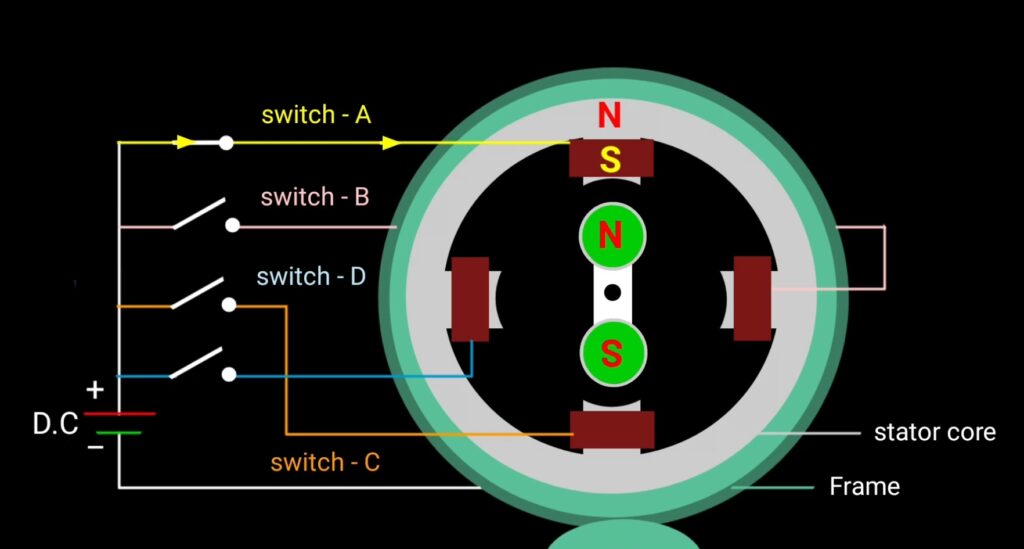
so current will flow only from switch-A. Due to the DC nature of current constant magnetic polarity produces on coil-A suppose (s-pole) develops on stator coil-A that will attract opposite polarity (n-pole) of the rotor and rotor align towards stator coil-A. Just like switch-A another switches will conduct one by one and another switches will be off , rotor will follow energize coil step wise. When switch-D will conduct conduct then another switches will be off
Opposite polarity of coil-D and rotor pole will attract to each other as a result rotor will align towards coil-D.
Thus when all phases innergize separately and rotor follows the energize phase and rotates step wise. In arrangement of four pole stator rotor is completing one revolution in 4-step , to complete one resolution in 8-step energize two pages together.
when coil-A and coil-B energize together then both S-Pole attracts the rotor N-pole with same force then rotor rotates at 45° angle

in this case rotor is completing one step with 45° so it will complete one revolution in 8-step. And if you want to rotate the rotor of stepper motor in anticlockwise direction then first coil-D will energize then coil-C then coil-B and then coil-A will energize, rotor will follow the energize Pole and it will rotate in anticlockwise direction.
Notes :
- since manually it is not possible to operate these switches that used in stepper motor
- so to innersize the different phases separately motor driver is used that supplies the voltage in required amount
- motor driver innersize the next phase according to rotor position and rotor follows the energize phase.
- Speed of a stepper motor controls electronically where controller is also include.
Step angle
step angle is the basic movement of stepper motor That depends upon number of poles in stepper motor. That is given by the equation..
[Ns – Nr/Ns × Nr] × 360
- Ns – number of stator poles
- Nr – number of rotor poles
suppose if we have stepper motor with ( Ns = 4 , Nr = 2 ) then what is value of step angle .
[4 – 2/4 × 2] × 360 = 2/8×360 = 90° is the step angle.